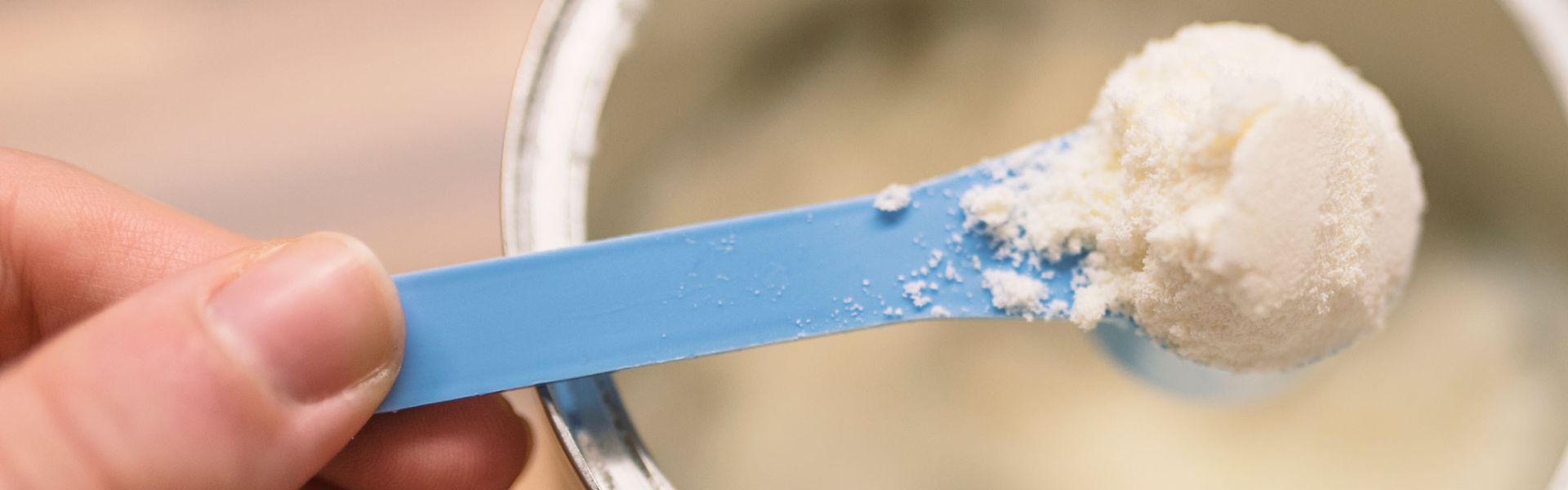
ANSES's recommendations on improving the control of microbiological hazards in powdered infant formula
Following the 2017 salmonellosis outbreak associated with the consumption of powdered infant formula, ANSES was asked to assess the hygiene, surveillance and control measures implemented in the manufacturing sector for these products, in order to improve the control of microbiological hazards. Following its expert appraisal, the Agency reiterates the importance of rigorously applying general hygiene measures to prevent contamination of formula. It also underlines the need to strengthen environmental monitoring of production sites and proposes some operational tools for this purpose. Lastly, the Agency recommends that the industry develop a guide to good hygiene practices and HACCP principles for this industrial sector.
Following the 2017 salmonellosis outbreak associated with the consumption of powdered infant formula, ANSES was asked to update its expert appraisal on the microbial contamination of powdered formula. The Agency based its work on the scientific literature and on an analysis of technical documents describing the measures taken by certain professionals to ensure the hygiene and safety of their products (health control plans). The analysis of the formula manufacturing process identified some potential routes of contamination and the main preventive measures.
Numerous possible routes of contamination
Powdered infant formula is a processed product that goes through many production steps and may be contaminated at different stages of the manufacturing process by bacteria found in the factory environment. The manufacturing steps generally include mixing the ingredients in liquid form, heat treatment (pasteurisation), drying, and adding ingredients before final packaging.
The two main microbiological hazards that can cause illnesses related to the consumption of powdered infant formula are Salmonella spp. and Cronobacter spp. Products can be contaminated after pasteurisation by bacteria present in the factory, or when ingredients are added.
Strengthen monitoring of the factory environment to ensure product safety
ANSES points out that the safety of formula depends on the rigorous and systematic application of general hygiene measures such as prevention of environmental contamination, analysis of ingredients, application of hygiene rules by staff, and cleaning.
The expert appraisal showed that checks of the finished product do not by themselves guarantee the safety of every batch. Indeed, a vast number of samples need to be collected and analysed to determine whether a batch is contaminated. However, these checks do make it possible to verify the effectiveness of the hygiene and prevention measures implemented in the factory.
The expert appraisal also proposed some sampling and analysis methods for testing finished products or the environment, along with their performance limits.
Monitoring and preventing contamination of the manufacturing environment are essential to ensure the safety of finished products. To achieve this, the experts proposed some tools for identifying contamination sources and routes, drawing up sampling plans for the factory environment (floors, walls, equipment, machinery, etc.) and searching for causes in the event of a non-compliance being detected.
Lastly, ANSES recommends that the industry develop a common guide to good hygiene practices and HACCP principles for the powdered infant formula sector.